Can Modern Methods of Construction & Offsite manufacture finally go mainstream?
- Jason Wild #TMC
- Mar 5, 2019
- 3 min read
Updated: Nov 30, 2024
By understanding the hurdles faced by clients, can architects help drive the future success of offsite construction?
With tragic events like Grenfell, public confidence in the construction industry is low and with a shortage of residential tenures, there seems no better time to embrace Modern Methods of Construction #MMC.
Despite the possibilities of offsite construction being available for decades it has struggled to gain significant traction up until now. But why historically has MMC failed to yet transform the mainstream housing market?
With the immergence of ground-breaking proposals for prefabrication in the 1930s and post-World War II, remarkably little has changed despite much effort within the industry until now - So perhaps we will start to see offsite manufacturing start to drive major change across the mainstream private housing market.

But for MMC to take off this time around, architectural innovation needs to be acutely aware of the hurdles in developing this as mainstream and it must be considered the architect’s job to study the challenges faced by clients and innovate around them.
A benefit to MMC that is often quoted is the speed of construction. However, in the private sale market it is not always a commercial advantage to bring all of your products into the marketplace at the same time. MMC would promote a far quicker delivery process, particularly with large developments, but this could lead to flooding the market, thus lessening the client’s ability to control sales values.
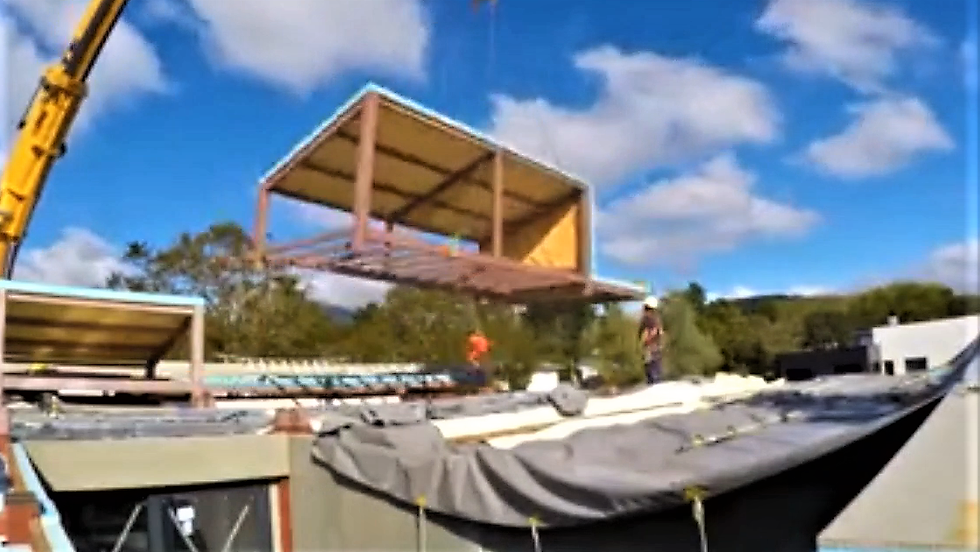
If the client is unable to benefit commercially from savings in time onsite, it becomes increasingly difficult to justify a cost premium that is normally associated with MMC when compared to traditional construction methods even if it is often more energy efficient.
For MMC to be financially competitive it will need to be able to scale up and fabrication plants will require significant investment. To overcome such issues, the industry needs to be very clear on the added value of MMC, in particular how it can promote high-quality design while still meeting all clients' demands.
Here are two reasons why we might have reached a watershed in MMC for housing.

Firstly, we have seen significant changes in the tenure of residential housing available in the market with the increase of the 'Build for Rent' sector.
This is set to increase to 40 percent of the market by 2025.
This offers a significant opportunity for MMC to move forward and develop their offsite manufacturing solutions.
The second is consumer confidence, with Grenfell putting the quality of building into sharp focus maybe we could finally see an end to all the integral parts still used with traditional methods and introduce the less risky development of facades under controlled conditions in a factory using the latest advancements instead.
Surely now, MMC is positioned well enough to start providing such a solution.

There is certainly a window of opportunity for architects to embrace what the MMC market can now offer and to try to capitalise on the opportunity through improvements in understanding between themselves and their clients.
The key to change in housing delivery is that architects can demonstrate to clients they are still able to deliver bespoke, high-quality products to suit all needs at all levels via these latest building methods but it is happening and the changes are apparent so maybe this time the conditions are advanced enough for it to be able to develop once and for all!?
Comentários